Terra Goyana Mining (TGM) benchmarks itself in mineral research, development, beneficiation and bauxite commercialisation, with its ore sorting strategy helping affirm these aims, STEINERT says.
Representing 5.5% of national production, TGM stands out among Brazil’s largest producers. It has operations at the Barro Alto mine (Goiás) and an office in Goiânia, and is part of the Supergram group, which operates in various sectors, including commercial bauxite extraction. Through Bautek, a producer of calcined bauxite, the group strengthens the vertical integration of its product.
To ensure a competitive product, TGM faces environmental, social and especially commercial challenges. The goal is clear: transform compact bauxite into a material with accepted calcium and aluminium content, to meet increasingly stringent market standards. With advances in mining operations, the need for innovative technological solutions has become even more urgent.
In this scenario, the implementation of sensor-based sorting (SBS) technology emerges as a solution to meet the market requirements, STEINERT says.
Previously, material classification was carried out through screening alone, which resulted in the retention of anorthosite a more resilient lithology rich in iron (Fe) and calcium oxide (CaO) in the coarser fractions.
As the next step in the project’s development, the creation of a new, higher-value-added product was planned. The primary requirement defined was to ensure efficient impurity removal to reduce calcium contamination below 0.15%. Additionally, increasing the aluminium oxide (Al₂O₃) content range between 62% and 63% would be beneficial, as it would enable the production of a premium material.
To accomplish this objective, developing a beneficiation flowsheet for the screened material would be required. Conventional bauxite processing flowsheets involve stages such as comminution, magnetic separation, washing, dewatering, or flotation.
It was in this context that the partnership with STEINERT Latinoamericana was established, providing SBS technology.
José Maurício, TGM’s Planning Manager, said: “The application of an ore sorter is crucial to meeting the requirements of specific markets, such as the refractory abrasives market, due to the strict standards regarding calcium oxide (CaO) content. With this innovation, TGM not only enhances its competitiveness in the industry but also positions itself as a benchmark in sustainable mining, aligning with best environmental practices and the growing global demand for more responsible operations.”
Innovation and concrete results
The collaboration between TGM and STEINERT began in 2022 with testing to validate the technology’s efficiency. Samples were sent to the Testing Centre in Matosinhos, Minas Gerais, Brazil, where STEINERT KSS | XT CLI equipment equipped with X-ray Transmission (XRT), colour, 3D laser and magnetic induction sensors were used to enabled precise material analysis.
In the first round of tests, using two 2 t of samples, from 1-4 inches, the results showcased a customised configuration for each material type, with a standout combination of XRT and 3D laser, ensuring highly efficient separation, according to STEINERT.
This initial success led to a second round of testing, focused on an even greater challenge: obtaining premium bauxite with high Al₂O₃ content while reducing contaminants such as silicon dioxide (SiO₂), hematite (Fe₂O₃), calcium oxide (CaO), and magnesium oxide (MgO), in a finer size fraction of 1-2 inches.
After finetuning the process, STEINERT’s technology, the company says, demonstrated its full capability to:
- Reject particles with high iron content;
- Significantly increase Al₂O₃ levels; and
- Reduce impurities to meet market standards.
The second test confirmed the efficiency of XRT technology in removing contaminants, achieving the desired parameters (CaO < 0.1%) and reducing Fe₂O₃ contamination in the reject material, which showed levels between 7% and 22%.
STEINERT says: “TGM’s strategy for directing ore sorter products reinforces the zero-waste concept, enabling the production of high-value bauxite and the commercialisation of reject material for various industries, such as cement, ceramics and metallurgy. This expands both sustainability and the economic feasibility of the process.”
Alexandre Rosa, TGM’s PCP Supervisor, said: “Bringing together the expertise of those who know the equipment with those who understand the process and the product allows us to identify the ideal operational limits and areas for improvement, facilitating collaborative work to optimise operational profitability and enhance the product.”
One of the improvements proposed by the STEINERT Latinoamericana team during the initial phase of the pilot plant was the use of object formation optimisation technology on its software to improve particle recognition and ejection accuracy. This helped counteract the effects of fines in the feed material while meeting the requirement to adjust the processed material’s particle size to 0.5-2 inches. As a result, data accuracy increased, result variability decreased and plant productivity improved significantly, according to the company.
Following this testwork, TGM acquired its first STEINERT sorting system, with Osmar Ribeiro, Beneficiation Supervisor at TGM, excited by the results: “By applying the sorter, we can leverage our production at the mining front, performing pre-classification of the anorthosite right in the sorter. This improved selectivity from the mining front to the crushing process, separating the anorthosite from the bauxite and during screening.”
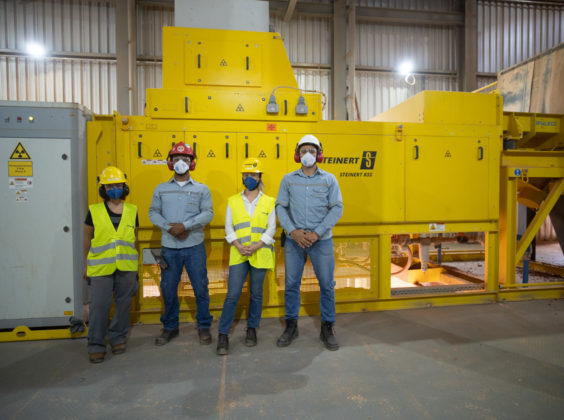
Solidifying the partnership
After more than a year of operation, the partnership between TGM and STEINERT has been strengthened, the company says. STEINERT provides continuous support, with remote assistance and regular technical visits to optimise processes and make personalised adjustments in line with new market demands.
Ribeiro says: “We rely on the excellent support from the technicians at STEINERT Latinoamericana who are in constant contact with me and the operators, always ready to correct failures — something common in any process, regardless of the time.”
During the assisted operation of the pilot plant, it was observed that the variation between the two predominant seasons – rainy and dry – directly impacts the efficiency of separation due to changes in the material’s characteristics. In response to this challenge, the STEINERT Global team actively worked to mitigate the production impacts and remains constantly attentive to provide support for the improvement of mineral operations.
As a result, the companies have established a solid partnership based on technical collaboration and continuous project development.
TGM’s process is 100% dry, using water only for infrastructure activities. This differentiator is fully aligned with the company’s ESG practices, reinforcing its commitment to more sustainable mining, STEINERT says.
It added: “With the implementation of the STEINERT Ore Sorter technology, TGM significantly increased the selectivity of the process, resulting in cleaner, higher-quality products that can be directed to new markets with more stringent requirements, without the need for wet beneficiation. Additionally, there was an increase in available reserves, as improving classification efficiency and ore recovery allows for better use of the deposit, thereby reducing future environmental impacts.”
The post STEINERT on transforming bauxite beneficiation with ore sorting appeared first on International Mining.