Anyone with their pulse on the mine electrification front will have been expecting an announcement from Brisbane-based BluVein before the quarter was out, and the company has now delivered that.
In what it is referring to as a “breakthrough in mine electrification” that leverages over 50,000 hours of engineering development, BluVein has introduced the third generation of its BluVein1 dynamic charging technology for underground mining vehicles.
The technology underpinning this new-generation platform consists of – at least in terms of hardware – a patented slotted (electric) rail system (BluVein Arm) that uses an enclosed electrified e-rail system mounted above or beside the mining vehicle (BluVein Rail) together with the BluVein Hammer that connects the vehicle to the rail. The system offers dynamic in-motion charging that can be used on hybrid, diesel-electric battery trucks or battery-electric vehicles (BEVs).
“It’s fast and cost-effective to install with lightweight rail sections placed exactly where haulage routes require,” the company says of the system. BluVein continues: “Power flows to haul trucks on demand, empowering them with zero downtime, allowing trucks to use smaller batteries and carry more payload.”
One of BluVein’s core objectives is accelerating the removal of diesel particulates from underground mining operations. “By enabling BEVs to charge while moving, BluVein’s dynamic in-motion charging technology enhances operational efficiency and significantly reduces the carbon footprint of mining activities,” it says. “Moreover, eliminating diesel from underground mines marks a major advancement in protecting miners from harmful diesel particulates, leading to healthier work environments.”
While legacy systems and BEVs are billed as offering this same diesel elimination benefit, BluVein states that the lack of flexibility and cost associated with existing trolley systems, and cost and limitations associated with the current crop of BEVs, mean they are not suitable for many deep, complex underground mines.
“Miners no longer need to rely on inefficient stop-to-swap or static charging methods,” it says. “BluVein’s slim line rail adapts to any haul route profile, including spiral declines. The system auto connects and disconnects, allowing trucks to charge seamlessly without interruptions.”
This concept has sparked interest in many miners, with BluVein collaborating with partners like Rio Tinto, BHP, Vale, South32 and Northern Star Resources on BluVein1 developments. The technology development has also attracted the attention of Epiroc, Hitachi Energy and Worley through separate agreements.
It was this type of flexibility – plus the ability to match if not improve on – current underground haulage productivity levels that first attracted Northern Star to this technology, according to Jeff Brown, General Manger – Technical Services.“We evaluated many different solutions when we started on our electrification and decarbonisation journey, carrying out a technology scan across the ecosystem,” he told IM. “Many of those technologies evaluated came with productivity trade-offs that made it hard to build an equitable business case, but we felt BluVein1 met the majority of our criteria and would compete with our current productivity levels.
“Not only that, but the technology also provided a pathway to full electrification, allowing us to start off in a ‘hybrid setup’ with diesel, or diesel-electric trucks, before transitioning to a fully-electric operation.”
He added: “Some other attractions to the technology were the compactness of the overhead solution and the flexibility of attaching to the overhead rail – allowing us to transition between ‘trolley off’ and ‘trolley on’ mode – as opposed to other, more rigid trolley-type systems that inhibit flexibility and may necessitate changes in, say, ramp conditions.”
A ‘modern trolley system’
BluVein is not only focused on the underground environment with BluVeinXL, a dynamic charging solution for 240-400-ton-payload trucks, suited to the open-pit environment. Leveraging off the underground-focused BluVein1 solution, this technology was one of the winners of the Charge On Innovation Challenge in 2022, and is now in the second generation, offering a reported 8 MW of power.
The company has carried out rigorous testing on its second generation prototype BluVein1 system, completing high-voltage, high-power tests at KEMA Labs in Germany, an independent testing, inspection and certification facility for the power industry.
Having concluded this testing and factored the learnings into a new design, the Gen 3 prototype is only a matter of months away from being installed on a vehicle to be tested at the BluVein Proving Grounds in Queensland, Australia: an open decline simulating an underground tunnel that is situated within an operating quarry. The proving grounds have already showcased BluVein’s advanced vision system, reliably detecting the rail’s proximity and enabling repeated, successful mechanical connections while the vehicle is in motion, the company says.
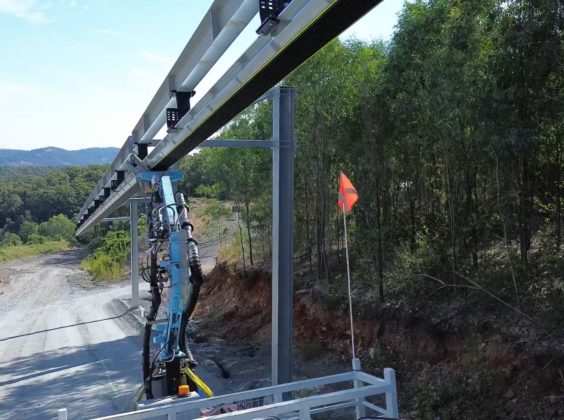
James Oliver, CEO of BluVein, said: “By the end of the year, we fully expect a diesel-to-battery-converted Epiroc Minetruck MT42 underground truck to be running with the system at the proving grounds.” An underground mine test is also in the works, IM understands.
This testing is part of an existing MoU between the two companies for pilot testing on the slotted electric rail system from BluVein, signed in 2022. At that time, the company said the collaboration provided Epiroc with the opportunity to extend focus beyond its own fleet and produce a dynamic charging solution which suited the needs of mixed fleet customers.
Anders Hedqvist, Head of Strategic Projects at Epiroc’s underground division, said the company still held the same opinion today, referring to the BluVein1 system as a “modern trolley system” that provides the company with different mining customer electrification options.
“We know electrification is the efficient way to decarbonise mining and we’re aware that battery-only options may not suit every application,” he said. “In terms of trolley, we don’t believe in only one solution; we are an OEM offering agnostic solutions, so the BluVein1 system gives us optionality when considering customers infrastructure and enabling mixed fleet operations.”
Oliver agreed with this sentiment, saying: “While the first machine may be an Epiroc truck, the system is very much OEM-agnostic; we have every intention of testing it out on other equipment.”
Scalability, flexibility and safety were just some of the associated BluVein1 benefits Hedqvist mentioned, which also matches well with the Epiroc portfolio of underground haulage equipment – which is being offered in battery-electric, diesel-electric and diesel options at the moment.
“We also potentially see the dynamic charging concept of BluVein1 offering a ‘hybrid’ option whereby the slotted rail could be installed on the ramp, for instance, as opposed to covering the entire underground production area,” he added.
Where the Minetruck MT42 converted truck is viewed as the “verification platform”, Hedqvist and Epiroc view the system as being applicable for all large trucks.
BluVein itself says the “1.5 MW-plus” charging capacity means it is the only OEM-agnostic dynamic charging technology capable of powering 60-plus-tonne underground haul trucks. This is important in a market like Australia that relies on these higher payload vehicles to keep up productivity levels.
Equally important is the safety element in a highly regulated market like Australia, with Oliver saying the Ingress Protection rated touch-proof conductors, plus electrical protection and earthing systems, were deemed vital by many of the companies BluVein has so far engaged with.
“The fact is regulators are only going to approve the use of new technologies that they deem low risk,” he said. “Even at this early stage, we see BluVein1 fitting into that category.”
Brown agreed with this assessment.
“When working in the vicinity of the actual rail system, the platform is being designed to be inherently safe,” he said.
“Being able to deliver those outcomes – productivity, flexibility and safety – all while having a high energy distribution system that can be used for our heavy haulage operations, is one of the elements that stands out with BluVein1.”
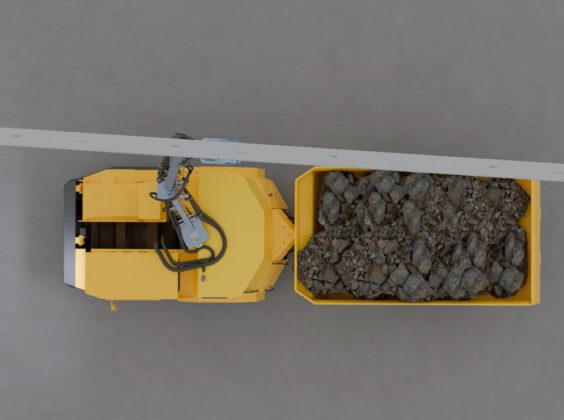
Brown and his fellow Northern Star technical team have been in the BluVein1 consortium for some time – at least since 2021 – and he said the technology has continued to answer all their questions as development milestones have been achieved.
“With every stage gate that the BluVein1 technology has passed, we have continued to baseline it against the rest of the decarbonisation and electric technologies out there and, to this point, nothing has matched up to it.”
Should BluVein be able to prove out all these mooted benefits, Brown sees huge change coming from the equipment makers looking to leverage the solution.
“The next logical piece is to say, ‘how do you optimise the vehicle that will be powered by BluVein1?’,” he said. “We’re now going to power that vehicle differently and use that vehicle differently, so: what should that vehicle look like?
“That question is hard to answer, but it’s fair to say that it is not going to look the same as a vehicle you’ve currently got on mines that’s based on a diesel engine, with a mechanical drive line and articulation points.
“What’s exciting here is the potential to build a vehicle around that system to make the most of the technology.”
The post BluVein1 dynamic charging system enters new territory appeared first on International Mining.