Sign up for daily news updates from CleanTechnica on email. Or follow us on Google News!
When BASF quietly backed away from signing a transport and storage agreement with Northern Lights for its Kairos@C project in Antwerp recently, it signaled more than just a missed customer for the high-profile Norwegian CCS initiative. It revealed the delicate balancing act at the heart of Europe’s carbon management ambitions: technical readiness, policy support, and commercial viability must align.
Northern Lights, a joint venture between Equinor, Shell, and TotalEnergies, has become the flagship cross-border carbon storage project in Europe. With Phase 1 designed to handle 1.5 million tons of CO2 annually, the project represents both infrastructure ambition and business model uncertainty. The roster of emitters who signed binding agreements—and those who didn’t—provides a window into how difficult it still is to make industrial carbon capture and storage work at scale.
I’ll be exploring Northern Lights in a short series of articles covering first the customers who signed up for it and their costs, then the transportation and its costs, and finally the facility itself and its costs. A summary article will wrap up the total cost structure and assess lessons learned. This was triggered by a European journalist reaching out to me last week to get my perspective on the shipping of the liquid CO2, as I’d published a nerdy analysis of one proposal for it a couple of years ago. I’ve been assessing CCS schemes for years, and they’ve never penciled out except with very big subsidies, and this is no different. It’s not very pretty or cheap, and these are among the best case scenarios for CCS.
The first two confirmed Northern Lights clients were domestic, Norwegian sources backed by strong government financial support. Norcem’s cement plant in Brevik, operated by Heidelberg Materials, is capturing roughly 400,000 tons per year using post-combustion amine capture provided by Aker Carbon Capture. The project includes full on-site liquefaction and a dedicated jetty for loading Northern Lights CO2 ships. The estimated capital cost of the capture installation is north of €350 million, translating to roughly €875 per annual ton of capacity. Operating costs remain high given the energy demands of solvent regeneration, solvent degradation, and maintenance needs for hot, dust-laden cement flue gas. Levelized capture costs are likely in the €120 to €150 per ton range.
The second domestic source, Hafslund Oslo Celsio’s waste-to-energy plant at Klemetsrud, also plans to capture around 400,000 tons per year. It too uses amine capture, albeit applied to a more complex flue gas matrix. Although this project faced significant delays and a redesign due to budget constraints, it ultimately moved forward using Aker’s modular Just Catch 400 unit. Capture costs are estimated in the same range as Norcem, though they may edge higher due to the variability of municipal solid waste feedstocks. Both projects have on-site buffer storage and direct loading to CO2 carriers or short pipeline connections to adjacent ports, eliminating overland trucking.
Yara’s Sluiskil ammonia plant in the Netherlands offers a very different profile. Capturing approximately 800,000 tons of CO2 annually from a high-purity process stream in ammonia synthesis, Yara’s project avoids the complex and costly flue gas cleanup required for cement and waste combustion. Instead, the main capital expense is in liquefaction and intermediate storage. Yara is investing approximately €200 million to build on-site liquefaction infrastructure. This equates to roughly €250 per annual ton of capacity. Operating costs are lower as well, with the CO2 stream already clean and dry. Capture costs, including compression and liquefaction, are likely under €50 per ton. Yara’s plant is located directly on the water, with its own quay on the Ghent–Terneuzen Canal in the Netherlands. The site is fully industrial and has direct maritime access, meaning liquefied CO₂ can be loaded directly onto Northern Lights’ ships from the plant without the need for overland transport.
Ørsted’s contribution to Northern Lights comes from two biomass-fueled CHP plants in Denmark, together delivering around 430,000 tons of biogenic CO2 annually. The company is deploying five modular Aker capture units across its Asnæs and Avedøre facilities, with a central CO2 hub at Asnæs serving as the liquefaction and export site. While flue gas from biomass combustion is generally cleaner than waste, it still contains oxygen and trace contaminants that require careful conditioning. Capital costs for these modular systems, including liquefaction and shared storage, are estimated in the €300–400 million range. Given the scale and modular nature, capture and conditioning costs may average €80–100 per ton, especially with Danish government support through a long-term contract for negative emissions. Ørsted’s Asnæs Power Station sits directly on the Kalundborg Fjord, with immediate port access for loading liquefied CO₂ onto ships.
Avedøre, near Copenhagen, lacks such access. Initially, the captured CO₂ from Avedøre will be transported by truck to the Asnæs facility, a distance of approximately 100 kilometers (62 miles), for liquefaction and subsequent shipping. This overland transport will traverse both densely populated urban areas of Greater Copenhagen and less populated regions as it approaches Kalundborg. There are plans to develop a shared pipeline infrastructure across Zealand in the future.
In 2020, in Satartia, Mississippi, a single CO2 pipeline rupture turned an ordinary night into a scene from a nightmare. A dense cloud of CO₂ rolled downhill into the town, displacing the air itself. Cars stalled as engines lost oxygen. People collapsed where they stood, gasping. Forty-five were hospitalized. And this happened in a rural area, with open space and low population density. The town’s entire population is 46, and it was 1.6 km away from the pipeline.
Ørsted’s Avedøre facility plans to send roughly 215,000 tonnes of captured CO₂ per year to its Asnæs hub. This volume translates to about 590 tonnes per day of dense-phase CO₂ flowing through a dedicated high-pressure pipeline expected to operate between 100 and 150 bar.
A full-bore rupture could release hundreds of tonnes of CO₂ rapidly, creating a cold, dense gas cloud that may remain near the ground and displace oxygen. In still weather, dangerous concentrations could spread over several hundred meters, with the most acute asphyxiation risks occurring within a 100–300 meter radius. The mat of CO2 would be 1-2 meters thick on level ground and it would pool in lower-lying areas to 3-5 meters thick. Children, pets, people sitting, and anyone in the lower lying areas would be at serious risk of asphyxiation. While rupture probabilities are low, such events require automatic shutoff valves, real-time monitoring, and emergency plans coordinated with local authorities.
Insurance coverage for this kind of infrastructure must include environmental liability, third-party injury, property damage, and loss-of-containment compensation. Permitting involves coordination with local municipalities, emergency services, and national agencies such as the Danish Energy Agency, Environmental Protection Agency, and Safety Technology Authority. These bodies will evaluate routing, safety systems, environmental impacts, and compliance with EU regulations, including the CCS Directive, the EIA Directive, and technical standards like ISO 27913. Approvals aren’t guaranteed, especially for municipal councils.
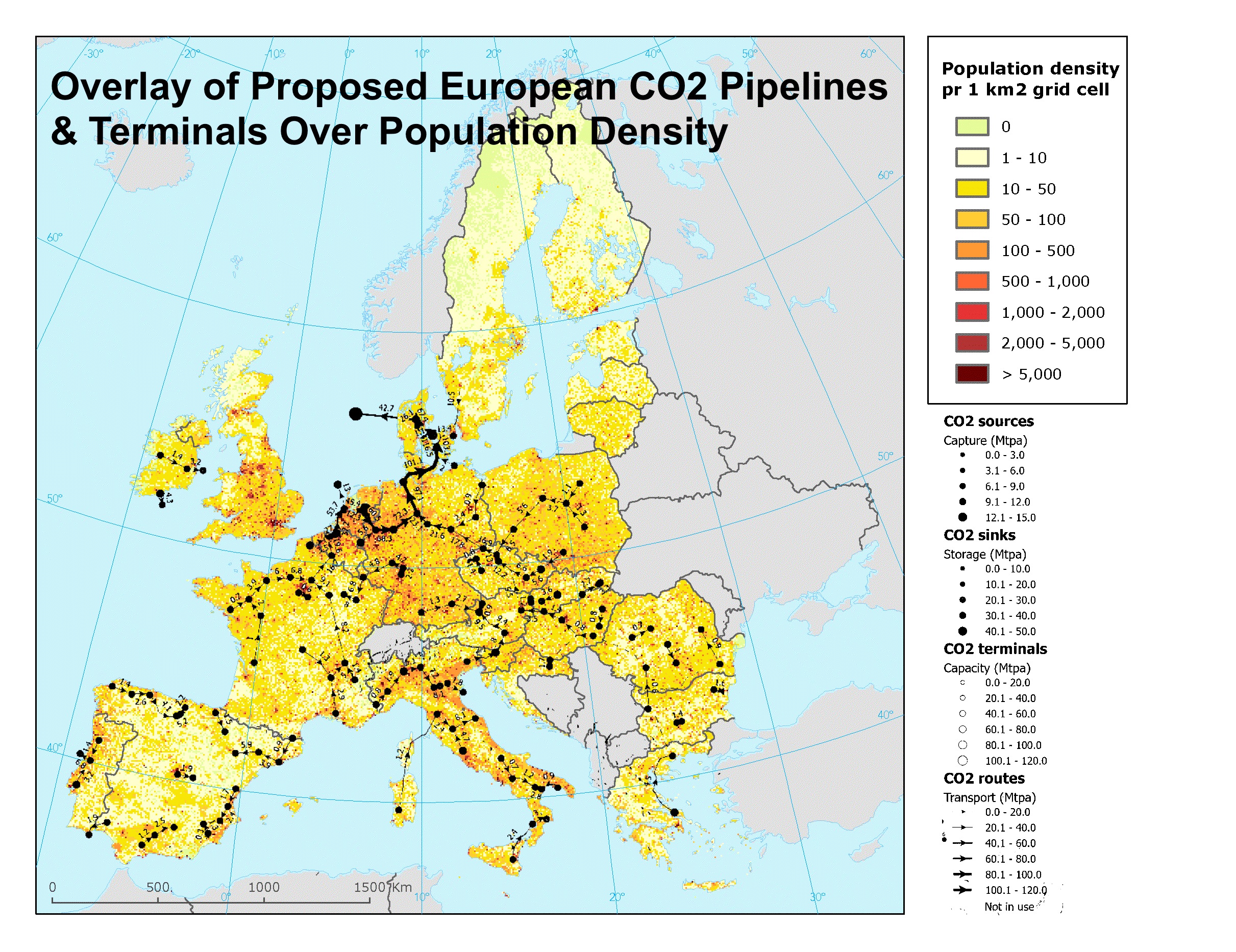
This is for a single, small, short distance, ~13 cm pipeline that only transports 590 tons a day. I developed the graphic above from a combination of Europe’s proposals for CO2 pipelines covering up to 19,000 kilometers overlaying population density maps of Europe, carrying millions of tons a day. I remain amazed that anyone thinks that this is going to be remotely acceptable to the citizens of Europe and takes this idea seriously.
Frankly, I suspect that the pipeline from Avedøre to Asnæs will never see the light of day, and the Avedøre CCS experiment will fail under the weight of the cost of trucking CO2, 20 tons at a time, will sink the project. It’s under active construction right now, so presumably they think they’ll be able to convince people that the pipeline is safe and will be able to build it, otherwise the costs wouldn’t have worked out.
The fifth client, Stockholm Exergi, will send up to 900,000 tons of biogenic CO2 annually to Northern Lights starting around 2028, under a 15-year contract. The CO2 will come from its biomass CHP facility in central Stockholm. Like Ørsted’s project, the flue gas is biogenic but urban. Stockholm’s plan includes full-scale capture, liquefaction, and storage tanks at its Värtaverket plant. Given the city location and large volume, capital costs are likely in the range of €400–600 million. Stockholm Exergi has secured substantial national and EU funding, and operational costs will benefit from integration with existing district heating infrastructure. Nevertheless, the overall capture and liquefaction cost is still expected to fall between €90 and €120 per ton. It’s right in a port too, so no concerns of CO2 leaks except for everyone at the facility, the ship crew, the port crew, and people living and working in the vicinity.
These five clients collectively fill Northern Lights Phase 1 capacity. More importantly, they illustrate the current viable archetypes for early-stage CCS in Europe: either high-purity process streams with modest capture cost, or politically-backed decarbonization of sectors like cement and waste with higher costs but strong state support. In both cases, they basically have to have a pipeline that runs straight into the water or have a big dock next to the facility for the CO2.
In this context, BASF’s decision not to proceed with a storage agreement for its Kairos@C project in Antwerp is informative. The Kairos@C project is designed to capture 1.5 million tons per year from several industrial facilities in the Port of Antwerp. While technically mature and partially funded by the EU Innovation Fund, the consortium including BASF, Air Liquide, and TotalEnergies is now exploring domestic storage options. They cite the potential of depleted gas fields in the North Sea closer to Belgium as an alternative to shipping CO2 to Norway, which I’ll explore in coming articles. This deferral or withdrawal removes a large-volume client from Northern Lights’ early portfolio.
While Northern Lights Phase 1 is fully subscribed without BASF, the loss of such a major emitter shifts the customer profile and reinforces the importance of public-sector intervention. Without government-backed Norwegian projects and generous EU co-funding for Stockholm and Ørsted, it is unclear whether Phase 1 would have reached financial close. The economics of CCS remain finely balanced. Projects like Yara’s demonstrate that low-cost, process-derived CO2 can be captured economically, particularly when liquefaction and port access are already in place. But for most emitters, especially those dealing with dilute or variable flue gas, per-ton costs remain above what EU ETS prices alone can justify.
From a risk management perspective, each of the five confirmed projects has internalized the need for CO2 purity, safe handling, and on-site buffer capacity. Liquid CO2 is stored at around -26°C and 15 bar, requiring double-walled tanks, boil-off management, and leak detection. The transport from capture site to ship loading terminal is typically short and controlled; overland trucking of CO2 has largely been avoided in Phase 1. This is not incidental. The safety risks of dense-phase CO2 in populated areas—asphyxiation in low-lying zones, brittle fracture in pipelines—are well understood and designed against. Where trucking is necessary, as in moving Avedøre’s CO2 to Asnæs, careful routing and vehicle design mitigate public risk.
The implications for future phases are clear. If Phase 2 scales to 5 million tons per year, Northern Lights will need to attract more emitters like Yara or secure longer-term state-backed contracts. The economics depend on consistent high utilization. The capital intensity of CO2 conditioning and liquefaction at each emitter site, combined with the logistics of safe transport and port infrastructure, means underutilized capacity can quickly drive costs per ton upward. In that context, BASF’s choice to wait for closer or cheaper options is rational. But it also underscores that CCS, even when technically ready, physically permitted, heavily subsidized and right next to water, is not yet an obvious solution. Every participant must see a credible path to recouping investment—and that path still depends heavily on public policy, subsidy, or carbon pricing.
For now, Northern Lights Phase 1 is a rare case of full subscription and multinational cooperation. But it is being carried, in large part, by Norway’s state-funded demonstration projects and European governments willing to bridge the gap between engineering feasibility and economic reality. That it required Yara’s cheap CO2, two domestic Norwegian plants, and three EU-subsidized BECCS projects to fill 1.5 million tons per year should temper expectations for rapid industrial-scale CCS rollout. The infrastructure is world-class, the technical risks mostly well managed, and the regulatory frameworks cooperative. But for most emitters, the missing link remains: who pays to make carbon disappear when the price of emitting it is still too low to matter?
Whether you have solar power or not, please complete our latest solar power survey.
Chip in a few dollars a month to help support independent cleantech coverage that helps to accelerate the cleantech revolution!
Have a tip for CleanTechnica? Want to advertise? Want to suggest a guest for our CleanTech Talk podcast? Contact us here.
Sign up for our daily newsletter for 15 new cleantech stories a day. Or sign up for our weekly one if daily is too frequent.
CleanTechnica uses affiliate links. See our policy here.
CleanTechnica’s Comment Policy