Entry-level fleet decarbonisation solutions are not yet falling off trees despite the industry’s lofty net-zero ambitions for 2050 and beyond.
Unless it is biodiesel – which has its own environmental detractors out there – there are only a handful of solutions that can be easily bolted on to make existing haul trucks or vehicles that much ‘greener’ than the diesel burning status quo.
Switch Technologies, a heavy-duty battery and electric vehicle engineering services provider, thinks it has just that with a solution more reminiscent of what has been seen in the automotive sector.
Switch states on its website, “We develop battery-electric drives that fit into the physical and commercial constraints of your existing operation,” indicating that it is aiming squarely at the retrofit market.
This was confirmed last year when the company, in tandem with niobium battery anode materials provider, Echion Technologies, unveiled a Toyota Land Cruiser 79 Series vehicle that has been modified into a plug-in hybrid configuration with a 24-kWh battery. This vehicle, which participated in a live track demonstration at the Australian Automation and Robotics Precinct (AARP) in Perth, Australia, on December 3, is equipped with cells manufactured by Li-FUN, an XNO® cell development partner. XNO anode chemistry enables lithium-ion batteries to safely fast charge in less than 10 minutes, maintain high energy densities even at extreme temperatures and deliver high-power across a cycle life of more than 10,000 cycles, Echion claims.
In the case of the Land Cruiser, this could see it complete around 90% of what is considered a typical underground shift for a light utility vehicle on battery power alone, according to Jan Haak, Managing Director and Chief Revenue Officer of Switch Technologies. He said this ability, which significantly removes the diesel emissions generated by an underground vehicle, plus the comfort level of being able to complete, say, a three-hour drive to go and pick up some parts, “resonated” with the mining community.
He expanded: “Add to these the innate safety characteristics that XNO offers – particularly the reduction in thermal runaway risk that the entire industry is aware of – while similarly enabling our customers to fast charge the battery in 5-6 minutes, plus offer all the quirks that operators have come to expect (wind-up windows, plastic floor coverings, etc), and we think we have a significant draw card on our hands.”
The ability to switch between battery, hybrid and diesel mode allows the flexibility and comfort that underground operations command.
In terms of the battery itself, Haak and Benjamin Ting, CCO of Echion, are confident it will outlive the demonstrator vehicle in question (which only had 150 km on the clock when Switch acquired it).
“The point of this XNO chemistry that Switch thinks brings value to a customer is how long it will last,” Haak says. “The battery is probably the only element of the Land Cruiser that we would recommend moving between multiple vehicles.”
The vehicle in question is expected to head back to the AARP this year for “stress testing”, Ting said, before potentially heading off to an actual mine site.
“Our goal with this testing is to really try and push it to the level where, within the calendar year, we know the real limits of this XNO chemistry in the hybrid Land Cruiser, and more generally, in hybrid vehicle applications,” he added.
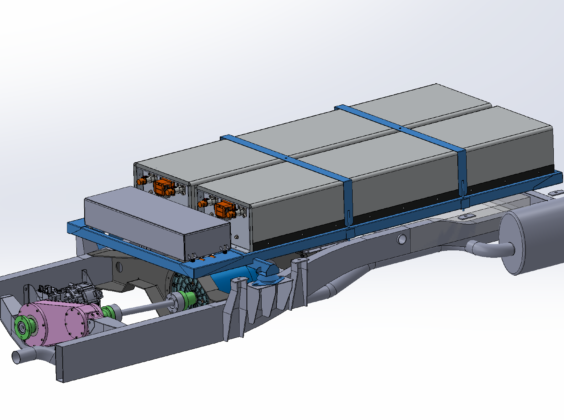
Heavier hybrids
This testing is also set to lay the foundations for an XNO-powered hybrid retrofit kit for much larger vehicles, specifically Caterpillar 785 and Caterpillar 789 trucks.
Haak explains: “Switch is a consultancy, so we’re working on a whole bunch of different and interesting projects and products, including on a heavy haul rail product for a US business. Alongside this, we’re also playing a significant role in bringing to market a hybrid mechanical drive Caterpillar 785 truck system, which is also able to support its bigger sibling, the Cat 789.”
Switch is currently developing the retrofit kit that can be equipped on both haul trucks, with agreements in place for “scaling the technology” with the necessary workshops and workforce, he added. Haak said a mining customer has already pledged one donor 785 vehicle to be fitted with a prototype kit.
The two vehicles, a 142-t payload Cat 785 and a 193-t-payload Cat 789, will require a bigger battery – Haak foresees it being around a 150-kWh battery pack – but possibly no stationary charging. Hitting this battery size, while maintaining high power regeneration and keeping the weight and volume in check, is uniquely enabled by XNO, the company claims.
Mike O’Hanlon, Founder and CTO of Switch Technologies, answers IM’s question on the required charge time like this: “It’s zero minutes. This is not a plug-in hybrid vehicle; it spends no time plugged in, charging up. It is purely regenerative.”
Haak says there isn’t anything to stop it being charged by an MCS or CCS-2 charger, but the idea behind the haul truck project is to remove the charging bottleneck, both in charge speed and infrastructure.
“Mike and his team sort of cracked through the calculations and realised that a haul truck going down a ramp in a cycle for anything like a 5-8 minute period would enable the majority, if not all, of the pack to be recharged with the right battery chemistry.
“That’s the key thing with a hybrid vehicle; it’s about getting as much energy in and out for as long as possible that it lives because that equates directly to the diesel offset.”
O’Hanlon says this decision has been taken directly from operators in the field.
“We have other projects we’re working on that will utilise megawatt charging systems, so it’s something our team is becoming increasingly familiar with, so that’s certainly not off the cards in terms of introducing that capability,” he said. “But the mines we’re talking to that want to deploy this technology in Africa, plus many of the ones in Australia, are coming to us to say, ‘We just don’t have a roadmap this side of 2030 where there will be enough energy and power on site to be able to charge a battery, or it’s going to be limited.’
“Being able to give customers the flexibility of potentially charging in the future is absolutely there, but there’s already a lot of energy on the table that we can take advantage of without even having to introduce the complexity of needing to charge.”
Not only is the company considering energy considerations, sustainability and productivity with this future offering; it is also taking capital expenditure into account.
O’Hanlon sums up his thoughts on this: “For the majority of mines that are operating a Cat 785, taking a kit like this is your most capital-efficient decision; you’re really just leaving money on the table if you’re not actively exploring offsetting some of that diesel burn.
“Burning 100% diesel with your haulage is definitely not the financially conservative move in 2025, but 0% diesel burn is typically not viable.
“We’re advocating for something in between.”
The post Switch Technologies aims for capital-efficient decarbonisation appeared first on International Mining.